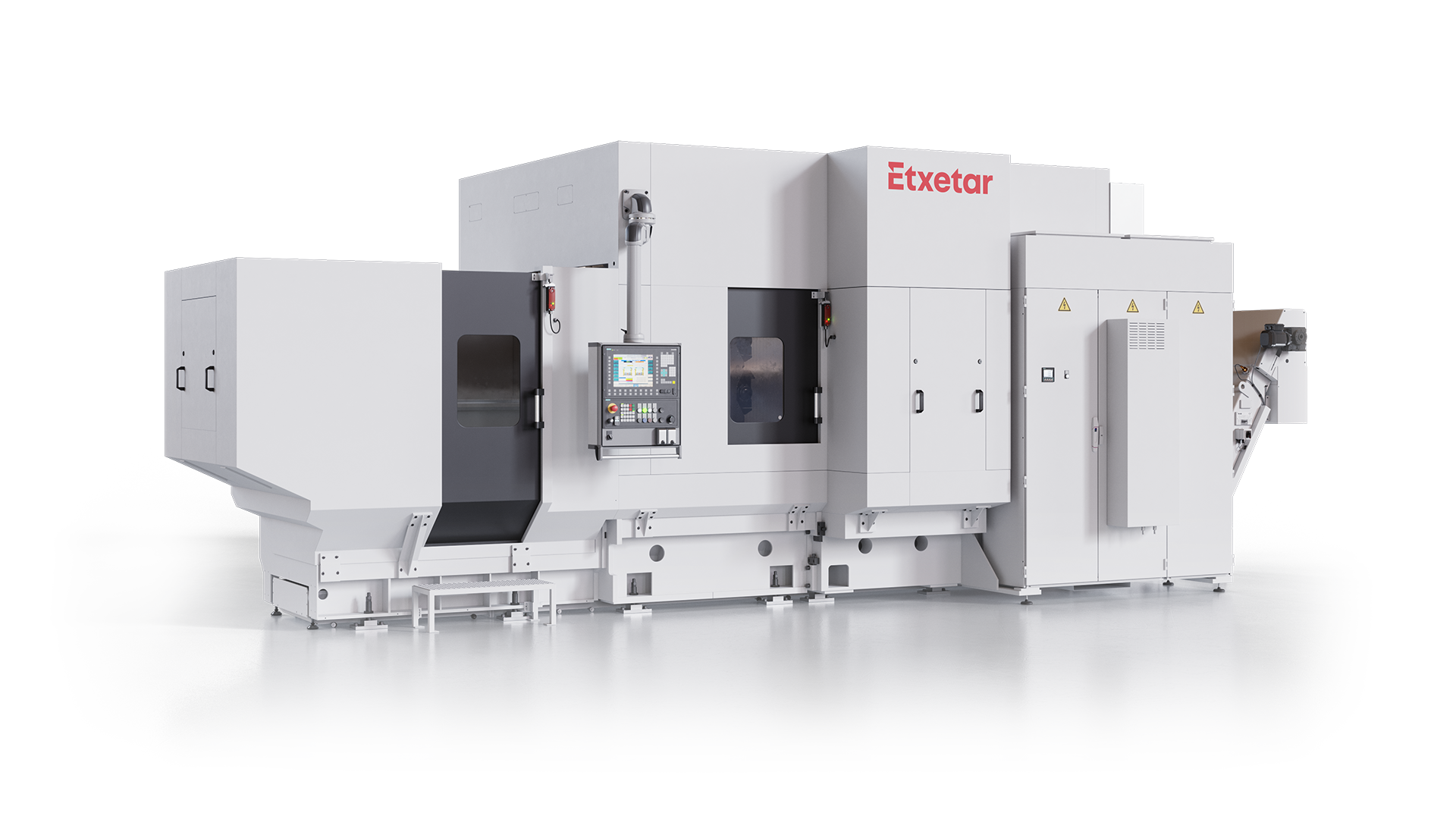
Xflex
Introduction
The Xflex series has been developed applying an extensive know-how of high productivity systems for steel, cast iron and aluminum parts.
From its initial conception as a deep hole drilling machine for crankshafts to its current form as a flexible machining center for various parts and operations, the Xflex series has undergone a profound transformation. Thanks to its modularity, these machining centers guarantee maximum stability and flexibility for high production environments.
And always with a single purpose: to provide our customers with a machine that is optimized to their specific part and operation.
- High adaptability to different production scenarios, by means of a modular platform that allows multiple spindles per machining unit, and up to two opposed machining units. Independent spindle Z axis available for twin spindle configuration.
- Multi-sided tombstone fixtures. The tombstone can be employed to ensure a quick and flawless change over, dedicating each idea of the tombstone for one part type or family. The tombstone allows us to overlap load and unload with machining operations as well, which in turn allows the reduction of the total number of machines required for your job.
- Compatible with Dry, MQL or high-pressure coolant machining.
- Design focused on favoring chip shedding.
- Ergonomic design for tool change and maintenance activities.
- Suitable configuration for gantry, robot, or manual load.
- 4 or 5 axes machining center. All linear axes provided with linear scales.
- Tool interface HSK-63, HSK-80 or HSK-100. Other interfaces upon request.
- Motorized or conventional spindle.
- Chain type automatic tool changer with 24 or 36 tools. Tool capacity can be upgraded upon request.
- Multiple tool breakage detection systems (laser, mechanical check, tool monitoring, etc.).
- Tool presence control in the tool exchange position between spindle and magazine.
- Unobstructed chip shedding designed for MQL machining.
- Totally sealed stainless steel front guarding with no horizontal surfaces.
- Honeycomb bed design so chips fall directly to the conveyor.
Machine architecture
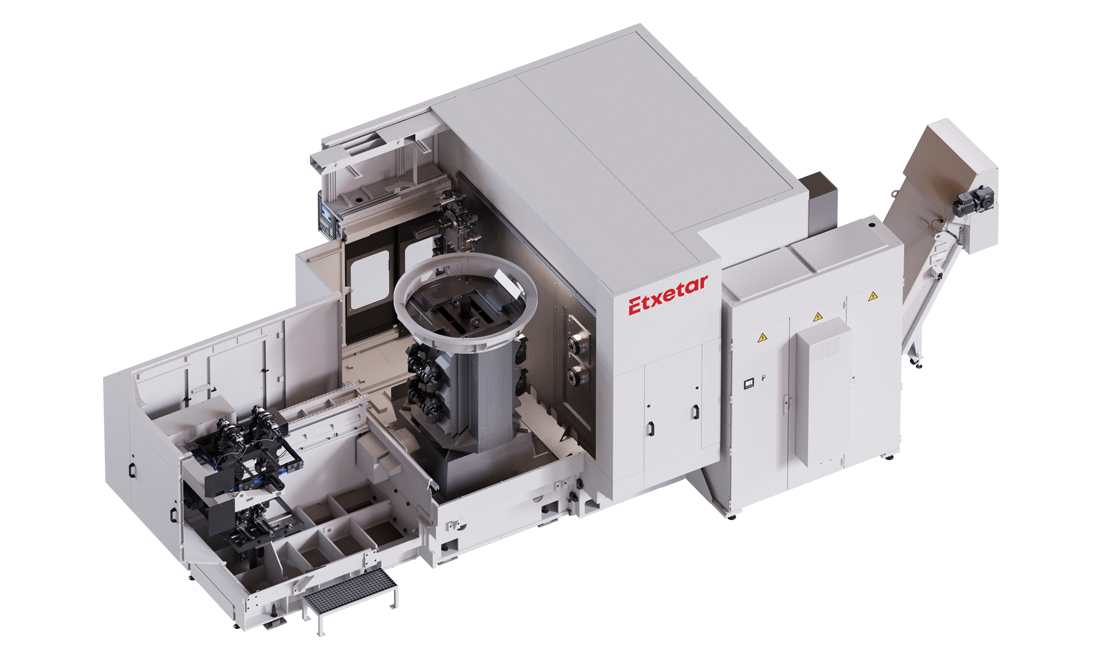
Fixture options
- 1, 2, 3 or 4 parts per fixture side.
- Limited by the part swing diameter and machining process tolerances.
- 1, 2 or 4 fixtures sides for flexibility or productivity purposes.
- Limited by the part dimensions.
- Axes: A / B / A+B NC motion in different fixture elements as an option.
- Zero-point locator cartridge fixtures as an option.
Machining unit
- 3 axis unit (X/Y/Z). 1, 2, 3 or 4 spindles.
- Limited by the part swing diameter and machining process tolerances.
- 1 or 2 units, depending on the production volumes.
Load/unload options
- Gantry load, by means of a loader integrated in the machine design.
- Robot load Manual load.
- Directly to the fixture or by means of a loader integrated in the machine design.
-
1 Fixture options
- 1, 2, 3 or 4 parts per fixture side.
- Limited by the part swing diameter and machining process tolerances.
- 1, 2 or 4 fixtures sides for flexibility or productivity purposes.
- Limited by the part dimensions.
- Axes: A / B / A+B NC motion in different fixture elements as an option.
- Zero-point locator cartridge fixtures as an option.
-
2 Machining unit
- 3 axis unit (X/Y/Z). 1, 2, 3 or 4 spindles.
- Limited by the part swing diameter and machining process tolerances.
- 1 or 2 units, depending on the production volumes.
-
3 Load/unload options
- Gantry load, by means of a loader integrated in the machine design.
- Robot load Manual load.
- Directly to the fixture or by means of a loader integrated in the machine design.
We can help you with the manufacturing process of many other applications